Share
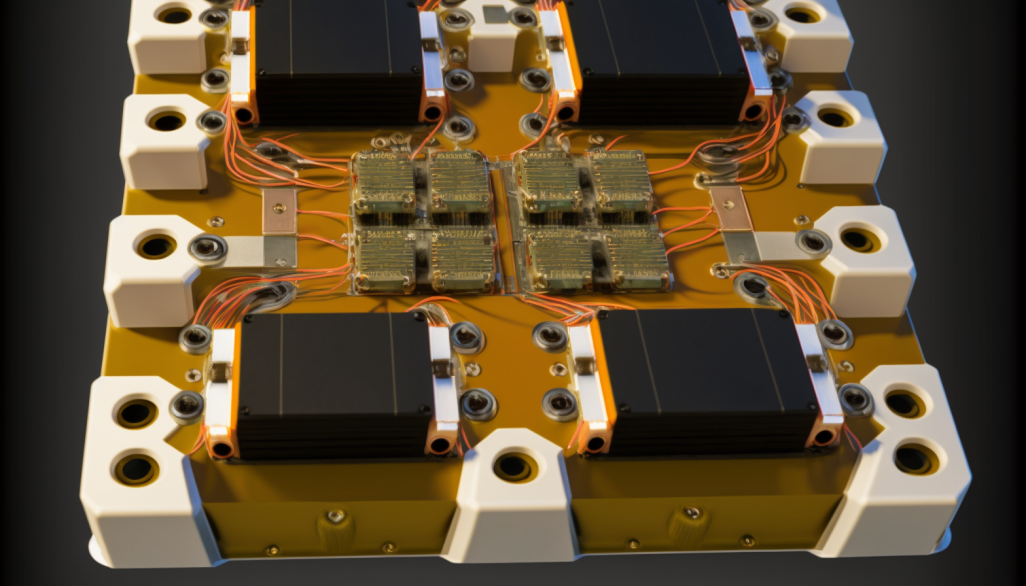
Metallized Ceramic Substrates for IGBT Module Production
IGBT (insulated-gate bipolar transistor) modules are semiconductor power devices widely utilized in high voltage and high current switching applications, such as electric vehicle drives, wind power generators, and UPS power supplies. The production process of IGBT modules includes various stages, such as semiconductor chip fabrication, encapsulation, casing installation, and testing. In the encapsulation process, metallized ceramic substrates play a crucial role in protecting and securing the semiconductor chips, enhancing their stability and reliability.
Metallized ceramic substrates are composite materials made of ceramics and metal, featuring advantages such as high-temperature stability, mechanical strength, corrosion resistance, and low dielectric constant. Their primary function is to provide excellent heat dissipation for the chips, protect them from damage, and enhance their stability and reliability. The quality and reliability of metallized ceramic substrates have a significant impact on the performance and lifespan of the entire IGBT module.
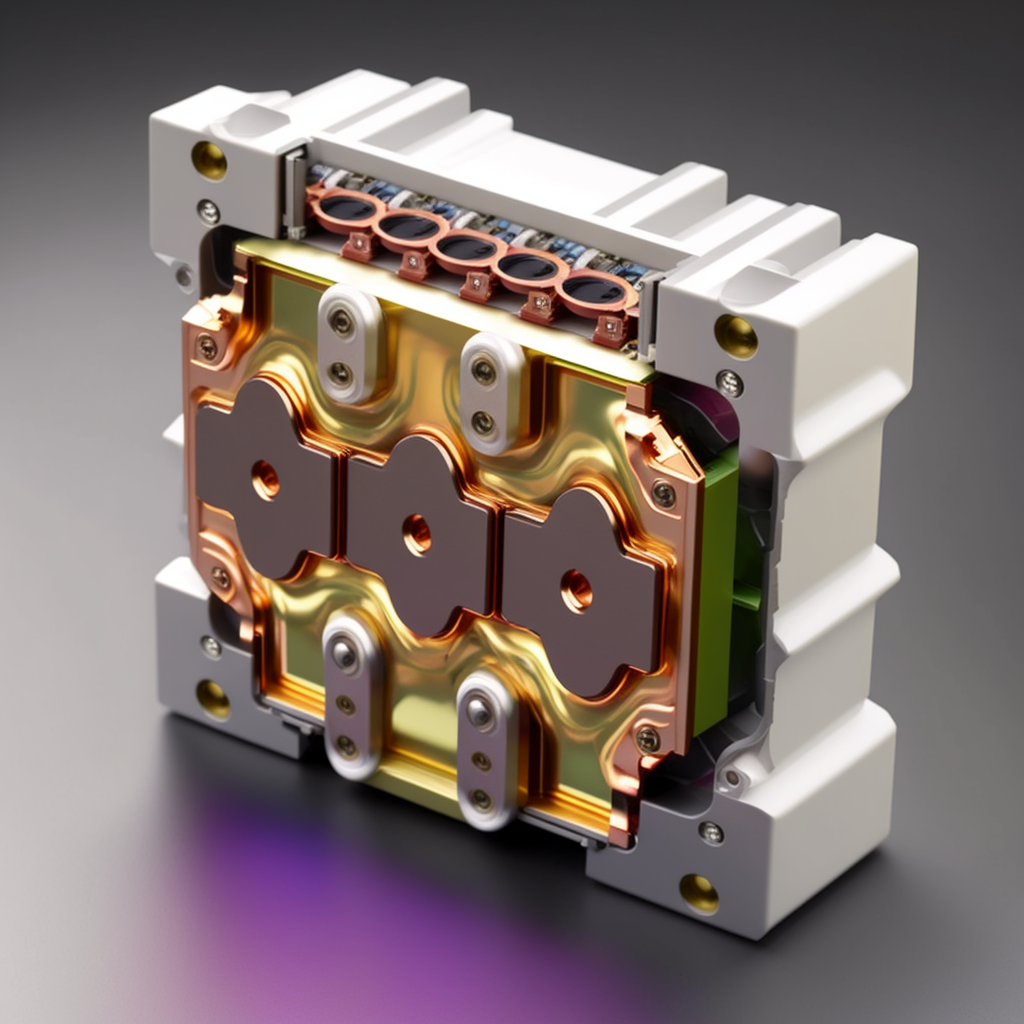
IGBT with metallized ceramic substrates
The production process of IGBT modules includes the following steps:
Semiconductor Chip Fabrication
Fabricate P-type and N-type semiconductor layers through processes like photolithography and chemical etching to form PN junction and control gate.
Semiconductor Chip Encapsulation
Place the fabricated semiconductor chips onto the conductive substrate, connect them with gold or copper wire, and add a protective layer.
Casing Installation
Mount the encapsulated semiconductor chips into the casing and fill the gaps with glue or filling material.
Testing
Test the IGBT module with the casing installed, including parameters such as voltage, current, and temperature, to ensure product quality.
Ceramic Metallization
During the encapsulation process, use metallized ceramic substrates to provide excellent thermal conductivity protection and secure the semiconductor chips, improving product stability and reliability.
Final Module Encapsulation
Fix the metallized ceramic substrates onto the module casing, then conduct terminal welding to complete the module production.
In the production process of IGBT modules, metallized ceramic substrates are mainly used in the encapsulation process to secure and protect the semiconductor chips. With the continuous development and promotion of technology, many new types of metallized ceramic materials have emerged to better meet various application needs, such as high-temperature alloy materials and special ceramic materials.
In conclusion, metallized ceramic substrates play a crucial role in securing and protecting the semiconductor chips, enhancing their stability and reliability, in the production process of IGBT modules. Cerametronics is a reliable choice for stable products, specializing in metallized ceramics and offering products with high frequency, speed, precision, stability, and temperature resistance. With the wide application of IGBT modules in various fields, relevant production technologies will continue to develop and promote the technology upgrade and development of IGBT modules.
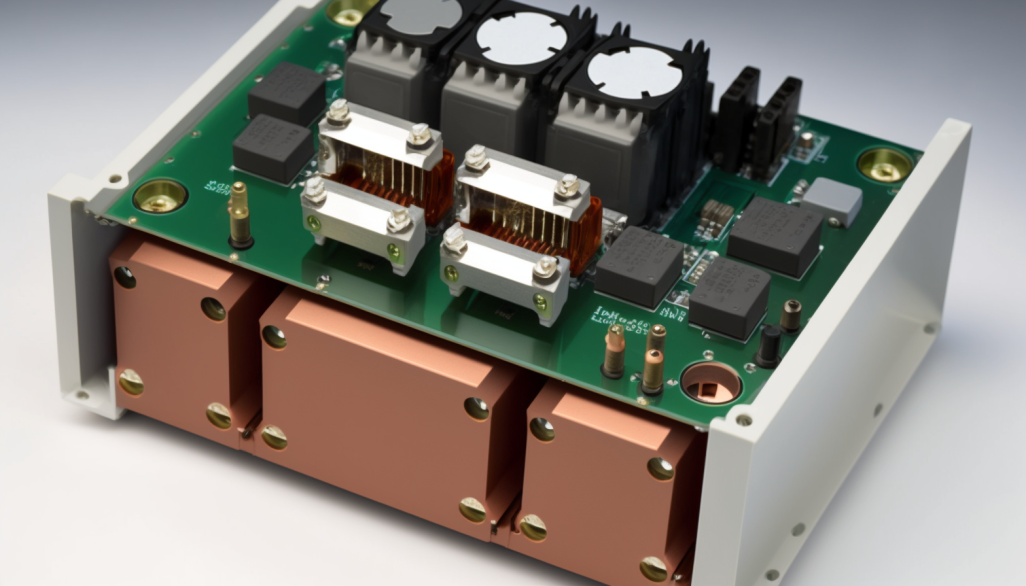
IGBT with metallized ceramic substrates
WELCOME TO Cerametronics
Cerametronics Is Your Reliable Choice For Stable Products.
We specialize in ceramic metallization, offering products with high frequency, speed, precision, stability, and temperature resistance. It is a reliable choice for stable products.
STAY IN THE LOOP